Cum se proiectează piese din plastic
Scurta descriere:
La proiectarea pieselor din plasticeste de a defini forma, dimensiunea și precizia pieselor, pe baza rolului pe care piesele îl joacă în produs și a regulii procesului de turnare a materialului plastic. Rezultatul final este desenele pentru fabricarea matriței și a piesei din plastic.
Fabricarea produselor începe cu proiectarea. Proiectarea pieselor din plastic determină în mod direct realizarea structurii interne, a costului și a funcției produsului și determină, de asemenea, următorul pas al producției, costului și ciclului matriței, precum și procesul și costul de turnare prin injecție și post-procesare.
Părțile din plastic sunt utilizate pe scară largă în diverse produse, facilități și viața oamenilor din societatea modernă. Piesele din plastic necesită forme și funcții diferite. Folosesc materiale plastice și proprietățile lor sunt variate. În același timp, există multe modalități de a realiza piese din plastic în industrie. Așadar, proiectarea pieselor din plastic nu este o sarcină simplă.
Designul diferit al pieselor și materialul sunt produse prin prelucrare diferită. Prelucrarea pentru turnarea plasticului include în principal mai jos:
1. turnare prin injecție
2. turnare prin suflare
3. turnare prin compresie
4. turnare prin rotatie
5. termoformare
6.extrudere
7. fabricarea
8. spumare
Există numeroase modalități de a le produce în masă. Turnarea prin injecție este o metodă populară de fabricație, deoarece piesele din plastic turnate prin injecție 50% ~ 60% sunt produse prin turnare prin injecție, este o capacitate de producție de mare viteză.
Vitrina pentru unele piese din plastic pe care le-am proiectat:
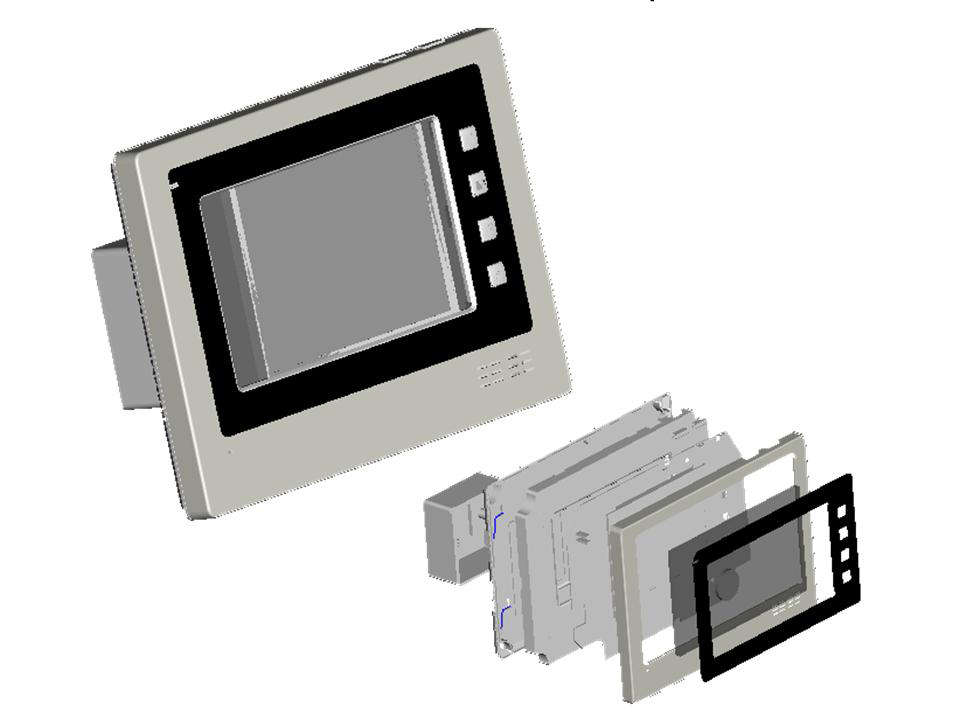
Carcasă din plastic a telefonului vizual
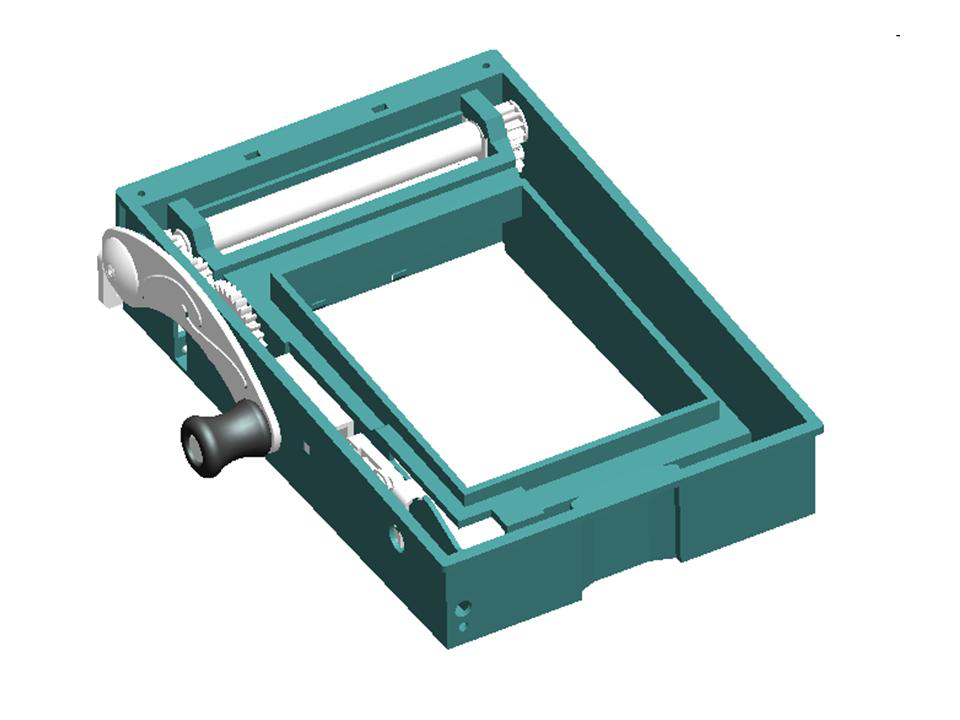
Părți din plastic ale mecanismului
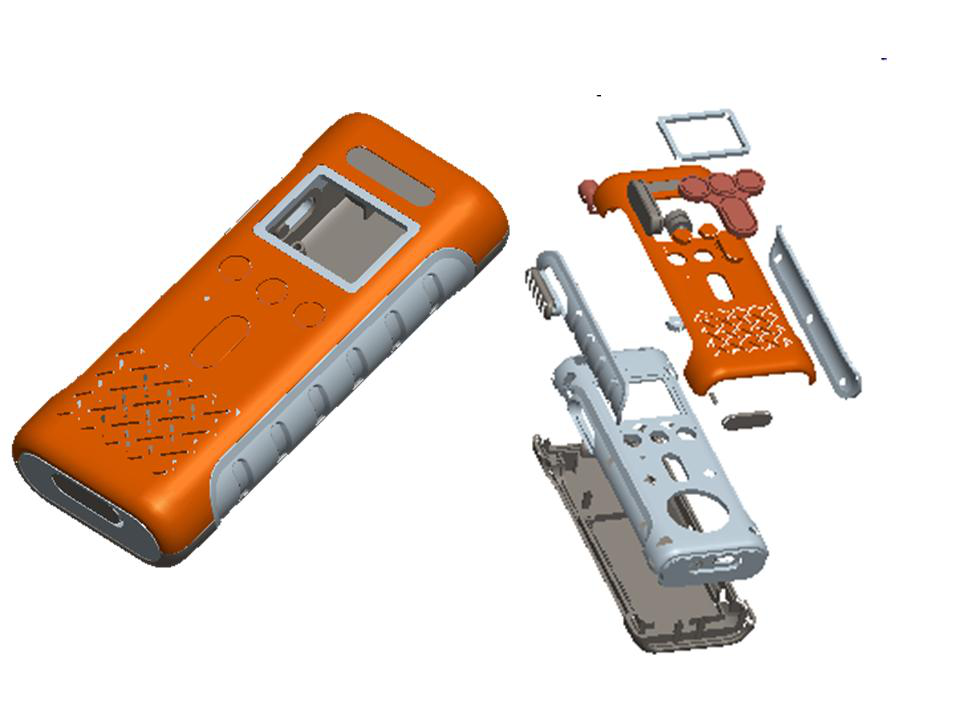
Cutii din plastic pentru electronice
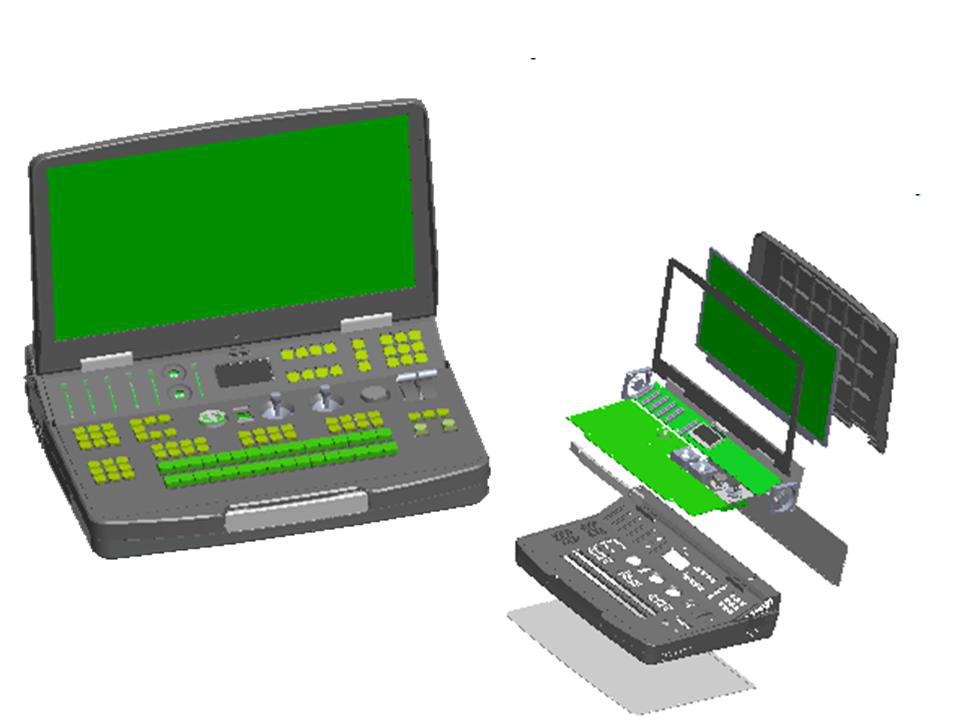
Carcasă din plastic pentru instrument
Mai jos împărtășim detalii despre cum să proiectăm piese din plastic în trei aspecte
* 10 sfaturi pentru proiectarea pieselor din plastic pe care trebuie să le cunoașteți
1. Determinați designul aspectului și dimensiunea produsului.
Acesta este primul pas în întregul proces de proiectare. Conform cercetărilor de piață și cerințelor clienților, determinați aspectul și funcția produselor și formulați sarcini de dezvoltare a produselor.
Conform sarcinii de dezvoltare, echipa de dezvoltare efectuează analiza de fezabilitate tehnică și tehnologică a produsului și construiește modelul de aspect 3D al produsului. Apoi, în funcție de realizarea funcției și de asamblarea produsului, sunt planificate părți posibile.
2. Separați piesele individuale din desenele produsului, alegeți tipul de rășină din plastic pentru piesele din plastic
Acest pas este de a separa piesele de modelul 3D obținut în pasul anterior și de a le proiecta ca individuale. În funcție de cerințele funcționale ale pieselor, alegeți materii prime din plastic sau materiale hardware adecvate. De exemplu, ABS este de obicei utilizat în
carcasa, ABS / BC sau PC trebuie să aibă anumite proprietăți mecanice, părți transparente, cum ar fi abajur, lampă PMMA sau PC, piese de viteze sau uzură POM sau Nylon.
După selectarea materialului pieselor, se poate începe proiectarea detaliilor.
3. Definiți unghiurile de pescaj
Unghiurile de tiraj permit îndepărtarea plasticului din matriță. Fără unghiuri de tiraj, piesa ar oferi o rezistență semnificativă datorită fricțiunii în timpul îndepărtării. Unghiurile de tiraj trebuie să fie prezente în interiorul și în exteriorul piesei. Cu cât este mai adâncă piesa, cu atât este mai mare unghiul de pescaj. O regulă simplă este de a avea un unghi de proiectare de 1 grad per inch. Lipsa unui unghi suficient de tiraj poate duce la zgârieturi de-a lungul părților laterale și / sau la semne mari ale știftului de ejector (mai multe despre aceasta mai târziu).
Unghiurile de pescaj ale suprafeței exterioare: cu cât este mai adâncă piesa, cu atât este mai mare unghiul de pescaj. O regulă simplă este de a avea un unghi de proiectare de 1 grad per inch. Lipsa unui unghi suficient de tiraj poate duce la zgârieturi de-a lungul părților laterale și / sau la semne mari ale știftului de ejector (mai multe despre aceasta mai târziu).
De obicei, pentru a avea o suprafață de aspect, textura se face pe suprafața pieselor. Peretele cu textură este aspru, fricțiunea este mare și nu este ușor să îl scoateți din cavitate, deci necesită un unghi de desen mai mare. Textura mai grosieră este unghiul de proiectare mai mare necesar.
4. Definiți grosimea peretelui / grosimea uniformă
Turnarea în formă solidă nu este dorită în turnarea prin injecție din următoarele motive:
1). Timpul de răcire este proporțional cu grosimea peretelui pătrat. Timpul lung de răcire pentru solid va învinge economia producției de masă. (slab conductor de căldură)
2) .Secțiunea mai groasă se micșorează mai mult decât secțiunea mai subțire, introducând astfel contracție diferențială, rezultând o deformare sau o chiuvetă etc. (caracteristicile de contracție ale materialelor plastice și caracteristicile pvT)
Prin urmare, avem reguli de bază pentru proiectarea pieselor din plastic; pe cât posibil grosimea peretelui ar trebui să fie uniformă sau constantă în exteriorul piesei. Această grosime a peretelui se numește grosime nominală a peretelui.
Dacă există o secțiune solidă în piesă, aceasta trebuie făcută goală prin introducerea miezului. Acest lucru ar trebui să asigure o grosime uniformă a peretelui în jurul miezului.
3). Care sunt considerațiile pentru a decide grosimea peretelui?
Trebuie să fie suficient de gros și rigid pentru treabă. Grosimea peretelui poate fi de 0,5 până la 5 mm.
De asemenea, trebuie să fie suficient de subțire pentru a se răci mai repede, rezultând o greutate mai mică a părții și o productivitate mai mare.
Orice variație a grosimii peretelui trebuie păstrată cât mai puțin posibil.
O piesă din plastic cu grosime variabilă a peretelui va avea rate de răcire diferite și contracție diferită. În acest caz, atingerea unei toleranțe strânse devine foarte dificilă și de multe ori imposibilă. Acolo unde variația grosimii pereților este esențială, tranziția dintre cele două ar trebui să fie treptată.
5. Proiectarea conexiunii între piese
De obicei, trebuie să conectăm două cochilii împreună. Pentru a forma o cameră închisă între ele pentru a plasa componentele interne (ansamblu PCB sau mecanism).
Tipurile obișnuite de conexiune:
1). Cârlige de prindere:
Conexiunea cu cârlige de prindere este utilizată în mod obișnuit în produsele de dimensiuni mici și mijlocii. Caracteristica sa este că cârligele de fixare sunt, în general, fixate la marginea pieselor, iar dimensiunea produsului poate fi redusă. Când este asamblat, este închis direct fără a utiliza instrumente precum șurubelniță, matriță de sudură cu ultrasunete și altele. Dezavantajul este că cârligele de prindere pot cauza mucegaiul mai complicat. Mecanismul glisor și mecanismul de ridicare sunt necesare pentru a realiza conexiunea cârligelor de prindere și pentru a crește costul matriței.
2). Îmbinări cu șurub:
Îmbinările cu șurub sunt ferme și fiabile. În special, fixarea șurubului + piuliței este foarte fiabilă și durabilă, permițând mai multe dezasamblări fără fisuri. Conexiunea cu șurub este potrivită pentru produse cu forță mare de blocare și demontare multiplă. Dezavantajul este că coloana cu șurub ocupă mai mult spațiu.
3). Montarea șefilor:
Conexiunea de montare a șoselelor este de a fixa două părți prin coordonarea strânsă dintre șosele și găuri. Acest mod de conectare nu este suficient de puternic pentru a permite dezasamblarea produselor. Dezavantajul este că rezistența la blocare va scădea odată cu creșterea timpului de demontare.
4). Sudare cu ultrasunete:
Sudarea cu ultrasunete se realizează prin punerea celor două părți în matrița cu ultrasunete și prin fuzionarea suprafeței de contact sub acțiunea mașinii de sudat cu ultrasunete. Dimensiunea produsului poate fi mai mică, matrița de injecție este relativ simplă și conexiunea este fermă. Dezavantajul este utilizarea matriței cu ultrasunete și a mașinii de sudat cu ultrasunete, dimensiunea produsului nu poate fi prea mare. După demontare, piesele cu ultrasunete nu mai pot fi utilizate din nou.
6. Tăieturi secundare
Subcutările sunt elemente care interferează cu îndepărtarea oricărei jumătăți a matriței. Subcutările pot apărea aproape oriunde în design. Acestea sunt la fel de inacceptabile, dacă nu chiar mai rele decât lipsa unui unghi de pescaj din partea respectivă. Cu toate acestea, unele subcotări sunt necesare și / sau inevitabile. În aceste cazuri, este necesar
scuturile sunt produse prin alunecarea / mișcarea pieselor în matriță.
Rețineți că crearea de subțiri este mai costisitoare la producerea matriței și ar trebui să fie redusă la minimum.
7. Sprijini coastele / gussets
Nervurile din partea de plastic îmbunătățesc rigiditatea (relația dintre sarcină și devierea părții) a piesei și crește rigiditatea. De asemenea, îmbunătățește capacitatea de mucegai, deoarece accelerează fluxul de topire în direcția coastei.
Nervurile sunt așezate de-a lungul direcției de solicitare și deformare maximă pe suprafețele neparențe ale piesei. Umplerea, contracția și ejectarea mucegaiului ar trebui să influențeze, de asemenea, deciziile de plasare a coastelor.
Nervurile care nu se unesc cu peretele vertical nu trebuie să se termine brusc. Tranziția treptată la peretele nominal ar trebui să reducă riscul de concentrare a stresului.
Coasta - dimensiuni
Coastele ar trebui să aibă următoarele dimensiuni.
Grosimea coastei trebuie să fie între 0,5 și 0,6 ori grosimea nominală a peretelui, pentru a evita marcajul chiuvetei.
Înălțimea coastei trebuie să fie de 2,5 până la 3 ori grosimea nominală a peretelui.
Coasta ar trebui să aibă un unghi de pescuit de la 0,5 la 1,5 grade pentru a facilita ejecția.
Baza nervurii trebuie să aibă o rază de 0,25 până la 0,4 ori grosimea nominală a peretelui.
Distanța dintre două nervuri trebuie să fie de 2 până la 3 ori (sau mai mult) grosimea nominală a peretelui.
8. muchii radiate
Când două suprafețe se întâlnesc, formează un colț. La colț, grosimea peretelui crește până la 1,4 ori grosimea nominală a peretelui. Acest lucru are ca rezultat contracție diferențială și tensiune turnată și timp de răcire mai mare. Prin urmare, riscul de defecțiune în service crește la colțurile ascuțite.
Pentru a rezolva această problemă, colțurile trebuie netezite cu raza. Raza ar trebui să fie furnizată atât extern cât și intern. Nu aveți niciodată colț ascuțit intern, deoarece promovează fisuri. Raza trebuie să fie de așa natură încât să confirme o regulă constantă a grosimii pereților. Este de preferat să ai o rază de 0,6 până la 0,75 ori grosimea peretelui la colțuri. Nu aveți niciodată colț ascuțit intern, deoarece promovează fisuri.
9. Proiectarea șurubului șurubului
Folosim întotdeauna șuruburi pentru a fixa două jumătăți de carcase împreună sau pentru a fixa PCBA sau alte componente pe piesele din plastic. Deci, șuruburile sunt structura pentru înșurubarea și fixarea pieselor.
Șurubul șurubului are o formă cilindrică. Șeful poate fi legat la bază cu partea mamă sau poate fi legat lateral. Legarea laterală poate duce la o secțiune groasă de plastic, ceea ce nu este de dorit, deoarece poate provoca semnul chiuvetei și poate crește timpul de răcire. Această problemă poate fi rezolvată prin legarea șefului printr-o nervură de peretele lateral așa cum se arată în schiță. Șeful poate fi rigidizat prin furnizarea de nervuri de contrafort.
Șurubul este folosit pe șef pentru a fixa o altă parte. Există tipuri de șuruburi care formează filet și șuruburi de tip tăiere a benzii de rulare. Șuruburile de formare a firelor sunt utilizate la termoplastice, iar șuruburile de tăiere a firelor sunt utilizate la piesele din plastic termorezistente inelastice.
Șuruburile de formare a firelor produc filete femele pe peretele interior al șoselei prin flux rece - plasticul este deformat local, mai degrabă decât tăiat.
Șurubul șurubului trebuie să aibă dimensiunile adecvate pentru a rezista forțelor de introducere a șuruburilor și sarcinii plasate pe șurub în funcțiune.
Dimensiunea orificiului în raport cu șurubul este esențială pentru rezistența la îndepărtarea firului și scoaterea șurubului.
Diametrul exterior al șefului trebuie să fie suficient de mare pentru a rezista la solicitările cercului datorate formării firului.
Alezajul are un diametru puțin mai mare la adâncimea de intrare pentru o lungime scurtă. Acest lucru ajută la localizarea șurubului înainte de a intra. De asemenea, reduce tensiunile la capătul deschis al șefului.
Producătorii de polimeri oferă instrucțiuni pentru determinarea dimensiunii șefului pentru materialele lor. Producătorii de șuruburi oferă, de asemenea, linii directoare pentru dimensiunea potrivită a găurii pentru șurub.
Trebuie avut grijă să se asigure îmbinări de sudură puternice în jurul găurii șurubului din șanț.
Ar trebui să aveți grijă să evitați stresul modelat la șef, deoarece acesta poate eșua în mediul agresiv.
Alezajul în șef ar trebui să fie mai adânc decât adâncimea firului.
10. Decorarea suprafeței
Uneori, pentru a obține un aspect frumos, facem adesea un tratament special pe suprafața carcasei din plastic.
Cum ar fi: textura, lucios, vopsire prin pulverizare, gravură cu laser, ștanțare la cald, galvanizare și așa mai departe. Este necesar să se ia în considerare în proiectarea produsului în avans, pentru a evita prelucrarea ulterioară nu se poate realiza sau modificările de dimensiune care afectează asamblarea produsului.